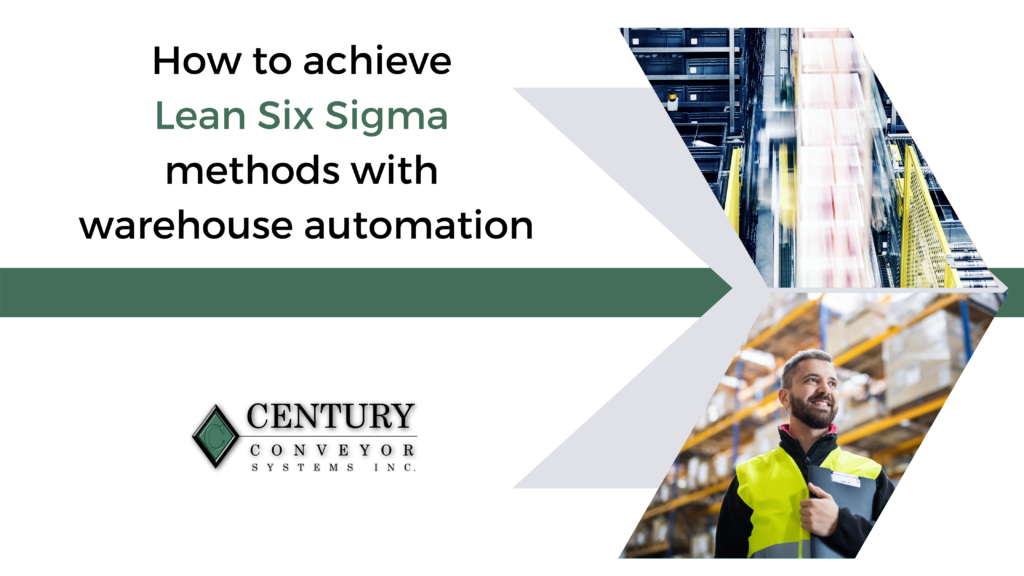
Lean Six Sigma is a powerful methodology practice designed to optimize operations and remove waste. It was created as a response to popular kaizen practices in the 1980s and has since been a staple in the industry. Its a tried-and-true guide to leaner manufacturing and processing has been adopted and applied countless times, to the point that executives are certified with Green, Yellow, and Black belts, signifying their experience with Lean Six Sigma. If you’re an operations professional in any capacity, you’re probably very familiar with these practices. If you need a bit of a refresher, here’s a great video from Simplilearn to get up to speed.
For this article, we’ll be applying Lean Six Sigma to post-production facilities, namely warehouses and distribution centers, with automation. Out of all the process improvements you can make to your warehouse, automation provides the greatest ROI, output rate, and stability. When working through Lean Six Sigma optimizations, automation is an excellent answer to avoiding waste and following lean techniques.
For the uninitiated, Lean Six Sigma uses the acronym DOWNTIME as a guide to each optimization point.
- Defects
- Over-Production
- Waiting
- Non-Used Talent
- Transportation
- Inventory
- Motion
- Extra-Processing
Defects
A product that has received damage or does not function. Defects can manifest at multiple points in a warehouse, for example, an old conveyor section that is known to jam and cause products to knock into each other, damaging them.
Modern automation uses a variety of photo eyes, sensors, and tracking to ensure products do not get damaged during warehouse movement. With the prevalence of product returns, keeping items safe and intact should be of utmost importance.
If the systems that your warehouse uses are not the issue, it may be a case of re-thinking your packaging strategy to include more void fill, or a sturdier carton structure (if you provide order packing). Integrating case erectors, sealers, or formers can provide fast, yet stable carton handling.
Unfortunately, defects can still occur when employees handle the products. Automating and eliminating manual operations will naturally reduce the risk associated with employee product touchpoints.
Over-Production
Eliminating waste is what applying lean six sigma methods are all about, and a major source of waste occurs when excess products are created, but simply take up space as they’re not being sold. While it’s always optimal to have a safety stock available in the event that demand for that item increases, it should be a carefully measured quantity based on product reports.
Avoiding costly over-production boils down to a visibility issue. Products continue to be manufactured at a nominal rate, but sales will always fluctuate.
Implementing a WMS, or warehouse management system, will give you incredibly invaluable clarity into inventory quantities, processing rates, and demand. Using this information, you can scale production accordingly, and interfacing the WMS data you acquire from the warehouse with ERP systems can assist your planning teams to make precise forecasts and informed product decisions, reducing waste caused by unsold inventory.
Waiting
Simply put, waiting in this light refers to any amount of time that waiting occurs due to an inefficient operation. This can span from something as simple as an employee waiting for an order to be picked, to as disastrous as a complete system failure that causes all employees to stop work and wait for the error to be corrected.
Product movement in a warehouse should be a continuous and streamlined operation. Actions should be staggered in a way that employees always have something to do and are not waiting on an action to be completed further upstream.
Automation can absolutely assist in this method, as one of the main goals of utilizing automation is to eliminate idle time. Let’s take, for example, a pallet that was received and is being inducted on a conveyor line. In a manual operation, employees must locate, transport, and depalletize the items. Downstream operators are waiting for this to be completed, sitting idle. If an automatic depalletizer arm was used in conjunction with either a pallet conveyor or an ASRS (automatic storage and retrieval system), the product flow would continue, and employees will always have products to process.
Sometimes, simply eliminating manual operations isn’t enough, in which case, empowering your warehouse workers can minimize times of stagnation.
Non-Used Talent
Much like the last method, spending time, money, and resources to have an employee complete a very simple task (like folding a box or stretch wrapping all day). Of course, automation can eliminate the need for such low-skill tasks, but human interaction will always be a part of warehouse operations. Properly training and equipping employees to co-exist with automation can cultivate talented and valuable workers in an upward trajectory.
Many automation solutions (primarily pick modules) can interface with wearable employee devices for efficient warehouse operations. Employees are more engaged, stay on task, and intimately learn to work side-by-side with automation.
Wearable devices can be wrist-mounted tablets synced with a WMS or WCS, voice-to-pick headsets, scanners, and even smart glasses. But practicing this method extends past providing tech to employees. Fostering an environment where learning is encouraged, combined with ergonomic automation solutions that rely on human interaction for the most optimal operation creates hard-working employees who feel valued and fulfilled.
Transportation
This method states that unnecessary or inefficient movements of people, products, and resources adds no value, and is a detriment to overall operational excellence. Think of a worker stacking pallets in the corner of the warehouse, only to have to spend precious time retrieving it when it must be processed.
Practically every usage of automation rectifies this method. A system will take the fastest and most efficient route in a warehouse, as it’s precisely engineered and planned to do so. Even equipment like racking helps expedite drawn-out transportation processes, keeping products organized, and maximizing space.
Typically, inefficient transportation is due to a lack of available warehouse space. This causes operators to use band-aid methods to accommodate. It may be time to consider expanding, or implementing space-saving solutions, like short-aisle rack structures, shuttle systems, extendable EOL conveyors, – or an ASRS.
Inventory
Inventory explains that over-compensating for demand and storing excess products is not conducive to a lean operating process. As mentioned before in the Over-Production method, using precious storage space for products that are not selling can be a source of gradual loss.
While mostly an item planning issue, implementing automation and storage solutions can help alleviate the constant ebb and flow of product demand. Maximize warehouse space using equipment like the aforementioned narrow-aisle rack, ASRS, or shuttle systems.
Regaining control of inventory so that items are always moving is a combination of having capable solutions, accurate quantity reports, and a product department that cross-tabulates with WMS reports. It cannot be understated how insightful a WMS platform is for informing forecast decisions, as the wealth of data it provides directly tells what is moving, and what is sitting stagnant and taking up space.
Motion
Much like Transportation, Motion instead focuses on the smaller movements that employees take with their tasks. Excessive motion due to an inefficient operation opens the door for lost time, errors, and safety risks. For example, imagine an employee at their pack station having to unjam an older taper machine multiple times throughout their shift.
Again, excessive motion by employees is typically due to faulty equipment or operations that must be compensated for. Retrofitting older equipment with newer solutions can help negate this but opening the lens wider to the entire layout of your warehouse can prove massively insightful in rectifying this Lean Six Sigma staple. Evaluate and re-engineer where key processing points are and decide if where newer systems can be placed or integrated to lower the amount of motion an employee makes.
Extra-Processing
This method focuses on doing excess work or using excess resources to fulfill a task. Essentially, not completing a function as lean as possible.
An example of this can be using packing products in cartons that are much too big, unused storage space, and even over-automation. For that last point, over-automation is very much possible and occurs when careful planning doesn’t take place. It’s when an automated system’s output is far greater than what the downstream warehouse operations can handle, resulting in excess product (in the case of a case erector, sealer, or former) or blockages.
Avoiding extra-processing with automation comes down to engineering a warehouse layout that is efficient and provides an increased rate of output but doesn’t produce more than operations can handle. It’s key to create practical processing rate goals and select an automation solution that works for the application. Consider the products that are being handled. A shuttle system works wonders for companies that store a large quantity of the same type of SKUs but would be overkill for a warehouse that doesn’t.
To practice this lean method, task a team of engineers, or work with an automation integrator to select an automation method that’ll fulfill all your process improvement needs, but doesn’t create an over-excess of products, resources, or work.
Lean Six Sigma is a valuable warehouse tool when automation is applied, even more so when solutions are carefully researched, engineered, and integrated. For decades, Century Systems has been innovating in the material handling industry by assembling all the pieces together in a solution that’s consistent with Lean Six Sigma methods, and your output goals.
Starting on an automation project can be difficult, and we understand this. Send us a message or give us a call and get in touch with an automation expert.