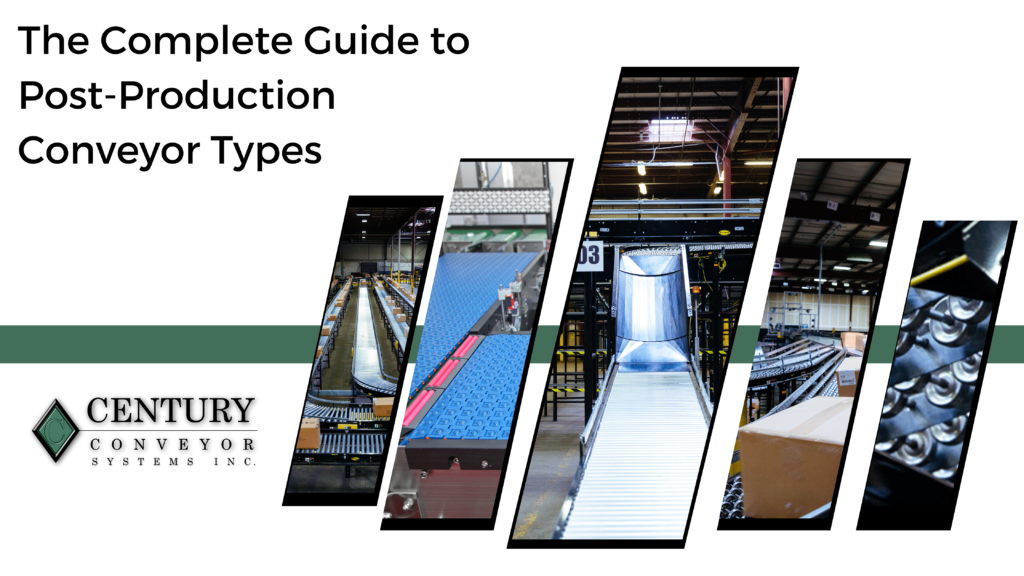
What is a conveyor?
Conveyor systems are a powerful material handling solution, offering a continuously moving platform to transport items quickly completing processing, sortation, and distribution. Conveyors typically use belts or rollers to move cartons or pallets, powered by motors, or by Earth’s gravity.
There exists a vast number of conveyor types, each specifically designed to handle certain materials or goods, spanning across a number of industries. For the purpose of this guide, we’ll be focusing on post-production conveyors, typically used in warehouses for distribution, and commonly seen moving cartons, totes, polybags, mail parcels, drums
Each warehouse has a specially engineered layout, consisting of a variety of conveyor sections, depending on function.
A few benefits of conveyors include:
- Durable and reliable, a well-maintained system can last over 20 years
- Various solutions can be added to a conveyor line to increase automation
- Conveyors offer the quickest form of transportation across a facility
- Split and full case order handling ability
Interested in a conveyor system for your facility?
Century Conveyor Systems has over 40 years of conveyor experience- planning, engineering, installing, and repairing post-production conveyor systems. Over the years, we’ve integrated systems ranging from a single line, to complex, multi-level operations. Want to discuss the goals you’d like to accomplish with a conveyor system? Send us a message to schedule a consultation.
What are the different types of conveyor?
Live Roller
The most widely used conveyor, live roller sections are powered by a motor. Instead of belts, live roller utilizes individual roller pins to transport product.
Gravity
As the name implies, gravity conveyors are not powered by any sort of motor, but simply by gravity. These conveyors are typically used in packing lines, divert lines, extendables, or EOL operations.
Belt-Over
Another common conveyor application, belt-overs utilize belts wrapped over the slider or roller beds. This allows a more stable approach to conveyance, especially for small polybags and parcels. Inclines, declines, and gapping are advantages belt-overs have over live-rollers.
Modular Belt
Operating in the same way as a belt-over section, modular belts are different when it comes to the material the belt is constructed of. Instead of vulcanized rubber, modular belts are plastic, and interlock with each other to accomplish different applications (like merging, sorting, descrambling, etc.).
Zero and Minimum Pressure
These accumulation conveyors are EOL solutions that utilize advanced sensor setups to provide gapping between items. This is to avoid products touching and causing damage and is used in situations where fragile items are conveyed.
Zero pressure indicates a line that will not let products touch each other
Minimum pressure indicates a line that will slow products down so they lightly touch each other.
Extendable
Extendables are telescoping conveyors that can be adjusted in specific situations, such as loading a truck or providing a temporary line. These solutions can come in flexible gravity-powered applications, using skatewheels to move product or as a powered outfeeding unit (like an Adjustoveyor).
Spiral
A spiral conveyor is named as such because it utilizes a gradual incline curve upwards in a spiral structure, to infeed to above-ground operations. Spirals are compact solutions to convey products to additional levels.
What are the different types of sortation conveyors?
Tilt-tray
Tilt-tray sortation uses order consolidation chutes to sort items in a batch-pick environment. Cartons are scanned before being inducted onto a tilt-tray carousel, where it will sit on a moving platform until it reaches its destination chute. The tray will tilt either left or right depending on where it’s being sorted and slide down a chute onto a conveyor to be loaded.
Tilt-tray applications are effective for high-speed sortation.
Cross-belt
Functioning similar to the tilt-tray, cross-belt sortation differs by using bi-directional belts to divert items into destination chutes. Packages are inducted onto the cross-belt conveyor carousel and sorted accordingly. Each belt section can hold one package, but multiple belt sections can be combined and used in tandem to divert larger items.
Narrow-belt
A series of narrow belts, each with its own take-up, span the length of the conveyor. High friction divert wheels rise between the belts, diverting product to its destination.
Narrow belts are typically used for larger, heavier packages that need heavy-duty forms of sortation. Smaller packages would not be ideal for this application, as they would fall in-between the belting segments.
Shoe Sorter
High-speed sorter utilizing aluminum slats that have plastic shoes that slide across them to divert cartons either left or right (bi-directional) to required sort destinations.
The advantage this provides over the similar functions of the tilt-tray is that the shoe is incorporated as part of the central induction conveyor. This eliminates the need for a separate sortation application, like the aforementioned tilt-tray carousel.
Split-tray Sorter
Sometimes also referred to as a bomb-bay sorter, dual split tray sorters have the ability to sort two smaller items within the same tray, at higher throughput speeds.
Split-tray sections have a bottom platform that opens to drop items gently into chutes, totes, or cartons below. This method is space-saving, as the item discharge area drops below vs being conveyed.
Swivel Wheel Sorter
Swivel wheel sorters utilize a platform of omni-directional rollers to divert items quickly. When a product reaches the divert, the wheels orientate to direct the item to its destination. This sortation method works best for systems that have a conveyor junction, rather than a gradual merge or curve.
Push-tray Sorter
A high-speed sorter with tray segments utilizing a positive divert to gently push items or polybags off the tray and slide them into a sortation chute.
What are the different types of pallet conveyors?
Pallet Drag Chain
These conveyor types support pallets and oversized loads. The item to be conveyed is placed on a platform that is connected to a chain. The chain is then activated and drags the platform along a conveyor section.
Pallet Gravity
Much like a typical gravity conveyor, the only difference in this application is the ability to handle pallets. A pallet gravity section is typically used for staging areas, or in EOL accumulation sections.
Chain Driven Live Roller
For high-output pallet operations, live rollers are ideal to provide the flexibility to move multiple pallets, using a drag chain to operate the rollers.
Poly-V
These powered live roller conveyors are designed specifically for stable, slow-moving bulk items. Poly-V sections are ideal for drums, lighter pallets, and oversized bulk loads.