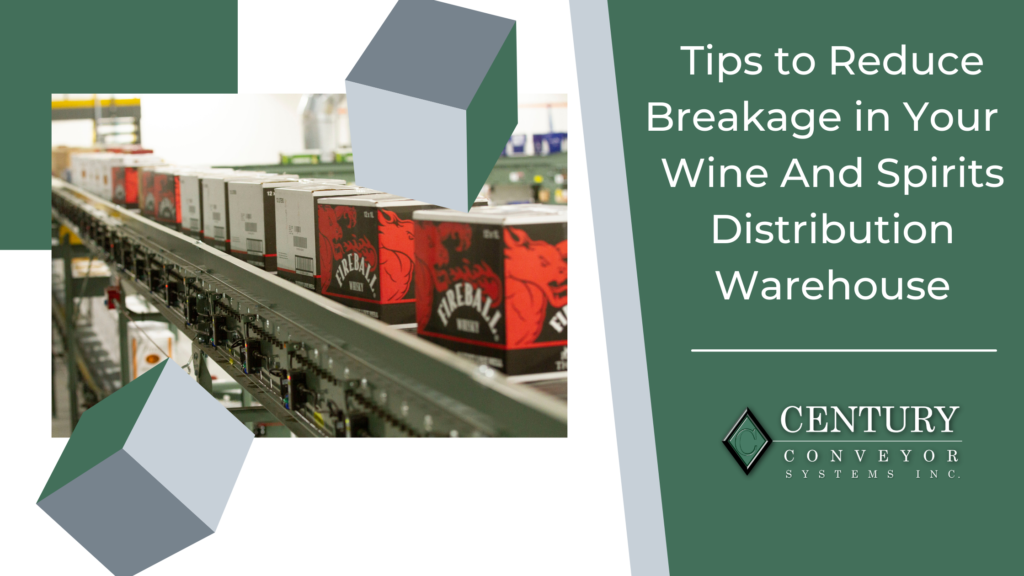
Product damage is a constant loss factor
The largest source of product loss in a wine and spirits distribution operation is undoubtedly bottle breakage and damage. Human error, product movement, and difficult storage methods can all be factors that result in damages.
In the case of one of Century’s wine and spirits clients, implementing our solutions resulted in a 75% decrease in product breakage. To give an example of how impactful that change is, imagine a distributor processing 30,000 cases a day. Each case, on average, is valued at $100 dollars. If their breakage rate is 1.25%, that’s $37,500 dollars lost on product damage from a total of $3,000,000.
A 75% decrease in the breakage rate would result in a much more manageable loss of $22,500- and that number can lower even more depending on the level of automation. That’s close to $5.5 million saved per year.
If your damage rate is on the higher end, it may be worth your time to evaluate your material handling operations. We have some valuable recommendations on where to look first.
- Indexing Belt Accumulation
- Warehouse Control Software
- Cascading Release Function
- Skewered Roller Design
- Telescoping Extendables
- Robotic Palletizing
- ASRS
1. Indexing Belt Accumulation
An effective method of preventing product breakage is the use of an indexing belt accumulation conveyor. These powered conveyors do not allow products to touch each other, using an array of sensors to properly gap infeeding operations, and stopping when the accumulation zone is full.
The product can be placed normally on the conveyor, and it’ll automatically speed or slow down zones to achieve safe spacing between each package.
2. Warehouse Control Software
Setting the operating parameters on a system play an important part in preventing product breakage. The software, depending on the system manufacturer, controls conveyor zone functions like speed, braking, idling, and more. When a system is first installed, or being upgraded, these settings are fine-tuned for efficiency and safety and can be easily changed in the future if need be. Warehouse Control Systems are versatile and offer a variety of customized system settings.
3. Cascading Release Function
A cascade release function staggers conveyor zones as the product begins to move. This provides a small gap between each product when operations start and stop. This function helps exponentially with end-of-line operations where a truck is being loaded, and the product is accumulating as it’s being moved from the conveyor to the bay.
Instead of the product pushing against each other, the conveyor can stop and move when space is available, to maintain proper gapping so that product never touches.
4. Skewed Roller Design (Herringbone)
To increase product safety, a skewed roller (herringbone) design can be used to avoid product from making contact with side railing and guards.
Skewed rollers are pointed diagonally inward, keeping cases positioned in the middle of the conveyor. Advancements in the packaging of alcohol mean solutions must accommodate a variety of carton dimensions and material types. Skewed roller designs provide additional flexibility and stability in any automated warehouse operation.
5. Telescoping Extendable
Typically, a warehouse worker picks up packages from an outfeeding source, walks over to the truck, and loads it. Even in this simple operation, it’s where most breakage mistakes occur, as employees can drop or jostle cases.
The solution is to eliminate the extra risk of having the worker walk over to the truck. A telescoping extendable conveyor attaches to an outfeeding source and can be operated so it extends into and out of the trailer as the worker loads. This allows for a much more stable operation and minimizes product damage by conveying the product directly to the worker, who places it into the trailer. Extendables can be simple skateroller conveyors on mobile casters or powered units such as the Adjustoveyor.
6. Robotic Palletizing/Depalletizing
For warehouses that use pallets, robotic palletizing solutions automatically handle and can build or deconstruct pallets. A wide variety of robots and end of arm tooling can accommodate most carton sizes and complex layer build configurations for pallets.
The speed and stability of robotic palletizing greatly outpace that of manual pallet building and even lift trucks. For further automation, completed pallets can be conveyed from a robotic cell to an inline stretch wrap operation, replacing tedious manual wrapping.
7. Automatic Pallet Storage
In warehouses that store a high volume of products, stacking pallets is a common sight. The issue is when pallets are being stacked over two high. This creates stress for cartons on the bottom of the supporting pallet, which could compress cartons, cause leakage, or topple the stacked pallets. The risk extends further when considering possible operator error in the action of stacking, such as dropping the pallet from too high or placing it unevenly.
Reducing breakage during storing and retrieving is best achieved by the usage of an ASRS (Automatic Storage and Retrieval System). An ASRS is a rack-supported structure with a track-mounted crane that can be programmed to navigate itself to a racking space to either remove or place a pallet. The advantages are clear, stacking does not need to be used, an automated crane is exponentially more accurate and stable than a forklift, and warehouse space is regained (as racking allows higher stacking, and the aisle for the cranes are thinner than typical racking structures).
Century Systems has extensive experience in integrating warehouse automation systems in the wine and spirits material handling industry. View the video below on a system we engineered and integrated with Fedway Associates.